External Capital Formation
Investor Capital
Investor Capital Structure
The following detailed analysis of the investor/shareholder base illustrates the investor-capital structure of the Company over the financial year 2013/14.
Shareholding as at 31st March 2014
From | To | No. of Holders | No. of Shares | % | |||
1 | 1,000 | 1,047 | 460,938 | 0.05 | |||
1,001 | 10,000 | 628 | 2,621,359 | 0.26 | |||
10,001 | 100,000 | 303 | 10,933,778 | 1.09 | |||
100,001 | 1,000,000 | 173 | 70,107,493 | 7.01 | |||
Over 1,000,000 | 45 | 915,876,432 | 91.59 | ||||
2,196 | 1,000,000,000 | 100.00 |
Categories of Shareholders
No. of Holders | No. of Shares | % | |||
Local Individuals | 1,993 | 802,115,100 | 80.21 | ||
Local Institutions | 156 | 168,057,436 | 16.80 | ||
Foreign Individuals | 36 | 17,950,736 | 1.80 | ||
Foreign Institutions | 11 | 11,876,728 | 1.19 | ||
2,196 | 1,000,000,000 | 100.00 |
Directors’ Shareholding as at 31st March 2014
Name | No. of Holders | % | |
Mr. S J S Perera | 250,000,000 | 25.0 | |
Mr. R J S Gomez | 120,000,000 | 12.0 | |
Mr. J C Joshua | 100,000,000 | 10.0 | |
Mr. S H S Mendis | 24,000,000 | 2.4 | |
Mr. D A R Fernando | 24,000,000 | 2.4 | |
Mr. S D Munasinghe | 24,000,000 | 2.4 | |
Mr. K A M K Ranasinghe | Nil | – | |
Mr. N D Gunaratne | Nil | – | |
Mr. A I Lovell | 16,000,000 | 1.60 | |
Mr. S D Perera | 2,000,000 | 0.20 |
Share Prices for the Year
Market Price Per Share | 2013/14 | 2012/13 | |
Highest during the Year | Rs. 23.50 (03.02.14) | Rs. 26.60 (02.04.12) | |
Lowest during the Year | Rs. 19.10 (08.04.13) | Rs. 13.50 (05.06.12) | |
As at end of the Year | Rs. 22.50 | Rs. 19.70 |
Public Holding
The percentage of shares held by the public 35.53%.
20 Major Shareholders of the Company
Name of Shareholder | No. of Shares | No. of Shares | ||||||
31.03.2014 | % | 31.03.2013* | % | |||||
1. | Mr. S J S Perera | 250,000,000 | 25.000 | 250,000,000 | 25.000 | |||
2. | Mr. R J S Gomez | 120,000,000 | 12.000 | 120,000,000 | 12.000 | |||
3. | Mr. J C Joshua | 100,000,000 | 10.000 | 100,000,000 | 10.000 | |||
4. | Mrs. R M N Joshua | 70,000,000 | 7.000 | 70,000,000 | 7.000 | |||
5. | Mr. S J S Perera | 46,000,000 | 4.600 | 46,000,000 | 4.600 | |||
6. | Mrs. D R S Malalasekera | 45,000,000 | 4.500 | 45,000,000 | 4.500 | |||
7. | John Keells Holdings PLC | 40,000,000 | 4.000 | 40,000,000 | 4.000 | |||
8. | Employees Provident Fund | 32,927,921 | 3.293 | Nil | Nil | |||
9. | Mr. S A A Gomez | 25,000,000 | 2.500 | 25,000,000 | 2.500 | |||
10. | (i) Mr. S D Munasinghe | 24,000,000 | 2.400 | 24,000,000 | 2.400 | |||
(ii) Mr. S H S Mendis | 24,000,000 | 2.400 | 24,000,000 | 2.400 | ||||
(iii) Mr. D A R Fernando | 24,000,000 | 2.400 | 24,000,000 | 2.400 | ||||
11. | Mr. A I Lovell | 16,000,000 | 1.600 | 16,000,000 | 1.600 | |||
12. | Associated Electrical Corporation Limited | 13,000,000 | 1.300 | 13,385,000 | 1.339 | |||
13. | J B Cocoshell (Private) Limited | 8,003,255 | 0.800 | 1,000,000 | 0.100 | |||
14. | (i) Barclays Bank PLC Singapore Branch (Wealth Management) | 8,000,000 | 0.800 | 8,000,000 | 0.800 | |||
(ii) Watapota Investments PLC | 8,000,000 | 0.800 | 8,000,000 | 0.800 | ||||
15. | MAS Capital (Private) Limited | 6,000,000 | 0.600 | 6,000,000 | 0.600 | |||
16. | Mr. R J Gomez | 5,000,000 | 0.500 | 25,000,000 | 2.500 | |||
17. | (i) Mr. S N F Irippuge | 4,000,000 | 0.400 | 4,000,000 | 0.400 | |||
(ii) Union Bank of Colombo PLC/ATSL International (Private) Limited | 4,000,000 | 0.400 | 4,000,000 | 0.400 | ||||
18. | AIA Insurance Lanka PLC A/C No. 07 | 3,453,332 | 0.345 | 4,961,359 | 0.496 | |||
19. | Mr. H A Van Starrex | 2,466,049 | 0.247 | Nil | Nil | |||
20. | Deutsche Bank AG-National Equity Fund | 2,277,925 | 0.228 | Nil | Nil | |||
881,128,482 | 88.113 | 858,346,359 | 85.835 | |||||
Others | 118,871,518 | 11.887 | 141,653,641 | 14.165 | ||||
Total | 1,000,000,000 | 100.000 | 1,000,000,000 | 100.000 |
*Comparative shareholdings as at 31st March 2013 of the twenty largest shareholders as at 31st March 2014.
Investor Relations
Investor Forums
Access Engineering undertakes regular investor relations activity as a matter of policy. In the year under review, members of the Board, including the Chairman, participated in all overseas investor forums hosted by the Colombo Stock Exchange (CSE). These events took place in India, Hong Kong, Singapore and the UAE.
Online Resources for Investors
Trading details for Access Engineering shares are updated daily in real time on the Company web site, www.accessengsl.com. The site contains a dedicated space for investors, giving access to annual reports, interim reports, research reports, changes in the constitution of the Board (if any) and other corporate disclosures, etc. More broadly, the site also details up-to-date operational information about the Company.
Release Dates of Interim Financial Statements - 2013/14
Due Date | Actual Release Date | |
Quarter 1 | 15th August 2013 | 2nd August 2013 |
Quarter 2 | 15th November 2013 | 5th November 2013 |
Quarter 3 | 15th February 2014 | 2nd February 2014 |
Quarter 4 | 31st May 2014 | 21st May 2014 |
The release of the Company’s 2012/13 Annual Report and its Annual General Meeting occurred in conformance with, respectively, the CSE’s Listing Rules and the Companies Act.
Release Dates of Annual Reports - 2012/13
Due Date | Actual Release Date | |
Annual Report | 31st August 2013 | 19th August 2013 |
AGM | 30th September 2013 | 12th September 2013 |
Dividends Policy
Subject to the provisions of the Companies Act No. 07 of 2007, and the Articles of Association of Access Engineering PLC, the actual amount and timing of dividend payments on the ordinary voting shares of the Company will be recommended and approved by the Board of Directors. The dividends policy of AEL will be based on a number of factors, including but not limited to the Company’s earnings, cash-flow position, future investments and funding of growth, the maintenance of a sound and efficient capital structure and any other factors the Board of Directors may consider relevant.
Earnings and Dividends Since Listing
2013/14 | 2012/13 | 2011/12 | ||||||||||||||
Group | Company | Group | Company | Group | Company | |||||||||||
EPS (Rs.) | 2.83 | 2.52 | 2.38 | 2.13 | 1.83 | 1.52 | ||||||||||
DPS (Rs.) | 0.50 | 0.50 | 0.50 | 0.50 | 0.27 | 0.27 | ||||||||||
Payout (%) | 18 | 20 | 21 | 23 | 15 | 18 |
An interim dividend of Rs. 0.25 per share was declared for 2013/14 and paid in full by the Company on 20th December 2013.
The final dividend of Rs. 0.50 per share was declared for 2013/14 on 8th July 2014 and is due for payment on 28th July 2014.
Performance of Shares
Comparative Performance of Shares - 2013/14
Relative to All-Share Price Index
31st March 2014 | 1st April 2013 | Change (%) | |
AEL Price (Rs.) | 22.50 | 19.50 | 15.38 |
ASPI | 5,968.3 | 5,705.2 | 4.61 | S&P SL 20 | 3,279.9 | 3,281.6 | (0.05) |
As shown, AEL has outperformed both market indices tracking the movements of the CSE.
Trading Statistics
31st March 2014 | 31st March 2013 | 31st March 2012 | |
No. of Shares Traded | 64,571,998 | 99,057,069 | 1,668,272 |
Value of Shares Traded (Rs.) | 1,265,038,262 | 2,147,640,644 | 45,103,518 |
Number of Days Traded | 239 | 243 | 4 |
Number of Trades | 13,535 | 10,229 | 975 |
Customer Capital
Customer Analysis
The two tables below present an analysis of sales made to external customers. Services provided on projects carried out by the Company are not represented.
In the discussion that follows, however, ‘customers’ are defined more broadly, to include both the public and private organizations that retain Access Engineering as a project contractor or subcontractor, as well as external customers, that is, customers for our engineering and allied services.
Customer Base (5 Year Analysis)
Sector | 2013/14 | 2012/13 | 2011/12 | 2010/11 | 2009/10 | |
Piling | 2 | 3 | 3 | 5 | 4 | |
Services | Mechanical and Steel Fabrication Workshops | 4 | 3 | 3 | – | – |
Geotechnical and Laboratory Services | 1 | 1 | 1 | 1 | – | |
Supply of Asphalt Concrete | 21 | 22 | 20 | – | – | |
Quarry Operations and Aggregate Production | 56 | 11 | 12 | – | – | |
Supply of Ready Mix Concrete | 38 | 40 | 5 | – | – | |
Engineering Designs | 1 | – | – | 1 | 2 | |
Products | Roads and Highways | 7 | 7 | 7 | 5 | 5 |
Bridges and Flyovers | 2 | 2 | 1 | 1 | 1 | |
Water and Wastewater | 5 | 4 | 3 | 3 | 3 | |
Building and Other | 4 | 4 | 3 | 2 | 3 | |
Airport and Aviation | 1 | 1 | 1 | – | – | |
Harbours and Marine Works | 1 | 1 | 1 | – | – | |
Dredging and Reclamation | – | – | 1 | 1 | – | |
Telecommunication Infrastructure | 3 | 2 | 2 | 1 | 2 |
Customer Turnover (Rs. Mn, 5 Year Analysis)
Sector | 2013/14 | 2012/13 | 2011/12 | 2010/11 | 2009/10 | ||
Services | Piling | 1,797.40 | 1,411.69 | 284.09 | 51.81 | 23.18 | |
Mechanical and Steel Fabrication Workshops | 52.52 | 20.19 | 1.60 | – | – | ||
Geotechnical and Laboratory Services | 0.89 | 9.75 | 2.98 | 4.00 | – | ||
Supply of Asphalt Concrete | 331.11 | 407.58 | 494.09 | – | – | ||
Quarry Operations and Aggregate Production | 31.30 | 53.37 | 55.31 | – | – | ||
Supply of Ready Mix Concrete | 84.44 | 162.00 | 1.58 | – | – | ||
Engineering Designs | 35.00 | – | – | 20.00 | 88.00 | ||
Products | Roads and Highways | 6,752.96 | 5,410.90 | 3,989.92 | 1,593.46 | 1,152.50 | |
Bridges and Flyovers | 761.63 | 241.41 | 17.93 | 667.01 | 364.12 | ||
Water and Wastewater | 869.09 | 967.76 | 472.76 | 325.73 | 550.56 | ||
Building and Other | 1,334.75 | 1,455.36 | 748.50 | 10.91 | 7.22 | ||
Airport and Aviation | 9.78 | 387.29 | 257.48 | – | – | ||
Harbours and Marine Works | 12.06 | 270.08 | 43.75 | – | – | ||
Dredging and Reclamation | – | – | 7.07 | 31.19 | – | ||
Telecommunication Infrastructure | 1,115.41 | 650.46 | 578.69 | 738.08 | 735.24 |
Types of Customers (3 Year Analysis)
Sector | Public | Private | Foreign | ||
Services | Piling | – | 1 | 1 | |
Mechanical and Steel Fabrication Workshops | – | 4 | – | ||
Geotechnical and Laboratory Services | 1 | – | – | ||
Supply of Asphalt Concrete | – | 20 | 1 | ||
Quarry Operations and Aggregate Production | – | 55 | 1 | ||
Supply of Ready Mix Concrete | 1 | 34 | 3 | ||
Engineering Designs | – | – | 1 | ||
Products | Roads and Highways | 3 | 1 | 3 | |
Bridges and Flyovers | 1 | – | 1 | ||
Water and Wastewater | 1 | 1 | 3 | ||
Building and Other | 1 | 2 | 1 | ||
Airport and Aviation | – | – | 1 | ||
Harbours and Marine Works | 1 | – | – | ||
Dredging and Reclamation | – | – | – | ||
Telecommunication Infrastructure | 1 | 2 | – |
Elements of Customer Value Creation
- The value engineering solutions provided by us to customers clearly differentiate us from our competitors. Recently, these have included composite flyovers, the installation of over 1,000km of fibre-optic cables island-wide for Dialog with minimum disruption to commuters, coffer dams, retaining walls, cable jetting and substructures. These solutions have resulted in expeditious construction and reduced costs.
- We have the highest accreditation from the Institute of Construction Training and Development (ICTAD) for most major engineering disciplines: C1 for buildings, highways, bridges, water supply and drainage, irrigation and land drainage, dredging and reclamation, groins and revetments; GP-B1 for piling; and EM1 for telecommunications. We thus possess the capacity to carry out civil-engineering works of any magnitude or complexity.
- Our in-house service portfolio is unmatched by any construction company in Sri Lanka.
- We are committed to sustainability, social, environmental and economic, and have adopted appropriate policies, standards and practices. Our corporate-citizenship activities and our efforts to improve the standards of our industry extend this commitment beyond the bounds of our commercial operations.
- Our corporate governance practices aim to broadbase company ownership, improve disclosure and increase transparency. Our 2012 listing on the CSE exemplifies this Independent and Non-Executive Directors sit on our Board and head our audit and remuneration committees. The Company Code of Ethics reinforces our commitment.
- Among our international partners, we have a reputation for resourcefulness, reliability and competitive pricing.
- Our service portfolio enables us to carry out specialized work customarily entrusted to foreign firms, helping save foreign exchange.
Enhancing Customer Value Creation
Capacity Building
We have continued to enhance our service portfolio over the years. We continued to use the new formwork system for building construction, field-testing methods including the static load-testing of piles and leak-detection methods.
Improvements to administrative efficiency and productivity also have knock-on benefits for customers. In 2013/14, these included the implementation of new enterprise resource planning and human resources management systems and a variety of different initiatives to conserve resources and reduce waste.
Over time, the results of our capacity building efforts have included business and profit growth, the expansion and modernization of our physical asset base and the ability to provide tax-free dividends to shareholders based on tax-free profits from the operations of our production plants.
Investments in Capacity Building, Rs. Mn (5 Year Analysis)
2013/14 | 2012/13 | 2011/12 | 2010/11 | 2009/10 | |
Land and Building | – | – | 30.44 | 8.43 | – |
Plant and Machinery | 115.33 | 955.58 | 1,114.00 | 275.99 | 34.73 |
Office Equipment | 66.06 | 18.20 | 22.93 | 7.14 | 16.55 |
Construction Tools and Equipment | 55.67 | 165.67 | 180.70 | 11.69 | 16.37 |
Motor Vehicles | 97.66 | 164.07 | 151.11 | 96.43 | 13.93 |
Furniture and Fittings | 55.93 | 9.50 | 30.94 | 1.88 | 1.96 |
Total | 390.66 | 1,313.01 | 1,530.13 | 401.56 | 83.54 |
Securing Business
For Access Engineering, a primary source of business has been the Government of Sri Lanka; many of our largest contracts have been infrastructure projects undertaken for this client. Such projects are awarded to contractors through a transparent tender process conducted by the respective authorities. Depending on the scope of construction, the nature of the project, the stipulated time frame and the available funding, Access Engineering will participate in the bidding process either alone or in partnership with internationally-reputed construction companies that possess relevant resources and expertise.
Access Engineering also works as a joint-venture partner with firms that have already secured infrastructure-development projects from the Government or other clients. Over the years, this practice has enabled us to develop strong relationships with leading international contractors and developers carrying out infrastructure projects in Sri Lanka. In some cases, we were instrumental in introducing these parties to clients in Sri Lanka; this often results, later, in the preferential award of subcontracts to the Company from these partners.
Many of the very large infrastructure contracts recently secured by the Company have come to us through joint ventures. Besides giving us the opportunity to demonstrate our capabilities and reliability as a partner, we gain both expertise and experience through these partnerships.
Responsible Design
As a contractor, we are usually required to follow designs created by architects and engineers separately retained by our customers, and to produce from them an end-product fit for purpose. To this end, we engage in constant dialogue with these designers of our products. We are keenly aware of our duty to bring to their notice designs or specifications that are not in accordance with current industry practices and standards, so that they can be modified accordingly.
All our construction activities are carried out in strict compliance with Sri Lankan and international standards, including those set by American, Australian, British and Indian authorities.
When a project calls upon our own design resources, we have a fully capable Design division, among whose personnel are several qualified engineers and chartered engineers. The team is reinforced by an experienced advisory consultant in the field of structural design. The capabilities of our Design division have enabled us to make the most of opportunities arising from the recent shift in the industry from construction contracting to design-and-build projects.
To help ensure product safety, designs produced by the Division are always reviewed by independent third parties, such as academics and other consultants with appropriate qualifications and experience.
Quality Assurance
The Company has in place a Quality Management System (QMS) compliant with ISO 9001:2008 standards. Quality assurance procedures are strictly followed. Measures to ensure effective quality control include the creation of quality standards, their implementation and employee training.
Quality assurance procedures and systems are subject to continuous improvement compatible with ISO 9001:2008 standards. They also undergo regular audits and reviews. During the reporting period, the Company’s Quality Management System and Environment Management System (EMS) were each subject to two audits by the regional certifying body.
The Geotechnical and Laboratory Services division is responsible for quality control during every phase of a construction project. During the year under review, Access Engineering obtained ISO 17025:2005 (general requirements for the competence of testing and calibrating laboratories) certification from the Sri Lanka Accreditation Board. The process, initiated in January 2011, was completed in April 2013 with the award of a Certificate of Compliance.
Regulatory Compliance Statement
- Total number of incidents of non-compliance with regulations and voluntary codes concerning the health and safety impacts of products and services during their life cycle, by type of outcomes: none.
- Total number of substantiated complaints regarding breaches of customer privacy and losses of customer data: none.
- Monetary value of significant fines for non-compliance with laws and regulations concerning the provision and use of products and services: zero.
Employee Capital
Investing in Our Employees’ Future
The Company’s new human resources information system, which became operational in December, has made HR Management at Access Engineering both more efficient and more responsive to the needs and potentials of our people. Its effects have been reinforced by the relocation of both Project Management divisions, formerly located at Boralesgamuwa, to our Colombo head office. Relocation has also facilitated the centralization of training and CSR activity. All aspects of legal compliance with respect to employees, too, have now been standardized and systematized.
Employee Statistics
Total Workforce by Employment Contract - 2013/14
2013/14 | 2012/13 | 2011/12 | ||||||||||||||||||||||||
Male | Female | Total | Male | Female | Total | Male | Female | Total | ||||||||||||||||||
Permanent | 38 | 16 | 54 | 36 | 16 | 52 | 35 | 14 | 49 | |||||||||||||||||
Contract | 1,188 | 94 | 1,282 | 1,194 | 91 | 1,285 | 1,110 | 88 | 1,198 | |||||||||||||||||
Casual | 1,151 | 83 | 1,234 | 1,780 | 128 | 1,908 | 1,804 | 123 | 1,927 | |||||||||||||||||
Total | 2,570 | 3,245 | 3,174 |
All employees of AEL are full-time employees.
Total Workforce by Category and Gender - 2013/14
Employment Category | Male | Female | Total |
Management and Professional | 134 | 26 | 160 |
Technical | 627 | 48 | 675 |
Clerical and Supportive (Operational) | 419 | 82 | 501 |
Skilled and Unskilled | 1,197 | 37 | 1,234 |
Total | 2,377 | 193 | 2,570 |
Total Workforce by Age Group and Gender - 2013/14
Age Group | Male | Female | Total |
18 - 20 | 22 | 4 | 26 |
21 - 25 | 253 | 22 | 275 |
26 - 30 | 633 | 41 | 674 |
31 - 35 | 363 | 34 | 397 |
36 - 40 | 628 | 39 | 667 |
41 - 45 | 183 | 48 | 231 |
46 - 50 | 172 | 5 | 177 |
51 - 55 | 92 | 0 | 92 |
Above 55 | 31 | 0 | 31 |
Total | 2,377 | 193 | 2,570 |
Total Workforce by Region - 2013/14
Province | Head Count |
Western | 1,590 |
Northern | 370 |
North Western | 588 |
Southern | 16 |
Eastern | 6 |
Total Head Count | 2,570 |
New Recruits by Gender
2013/14 | 2012/13 | 2011/12 | ||||||||||||
Male | Female | Male | Female | Male | Female | |||||||||
160 | 48 | 234 | 63 | 1,607 | 88 |
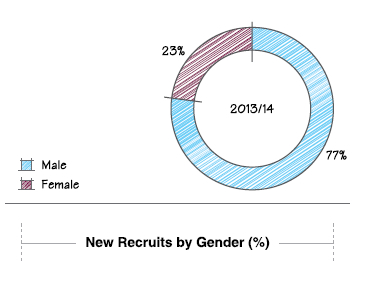
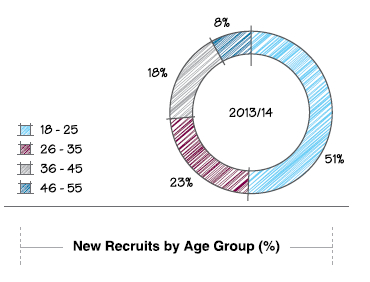
New Recruits by Division - 2013/14
Division | Number of Employees |
Head Office | 18 |
Project Management Division I | 85 |
Project Management Division II | 63 |
Project Management Division III | 42 |
Total | 208 |
Employee Benefits
Employees of the organization enjoy benefits such as insurance schemes, annual bonus, annual profit share, vehicle allowances, staff loan facilities, festival advance etc. These benefits may vary depending on the employee grade.
Training and Development
A structured approach is used to determine the training and development needs of our people and to devise appropriate programmes based on them. Training is conducted in the following areas:
- Technical skills
- Management systems
- Leadership skills
- Soft skills
- Personal development
Programmes are conducted by an internal panel of skilled and qualified trainers, and are evaluated in terms of trainee reaction, learning, practical application and results achieved.
We are now in the process of developing a competent systems management team to conduct ISO 9001, ISO 14001 and OHSAS 18001 system audits. Members of this team will also conduct the staff training and guidance necessary for the implementation of these systems.
We offered industrial placements to a total of 151 students pursuing vocational or technical studies at university and other formal institutes in the year under review.
The quality of our training and development initiatives was recognized at the 2013 People Development Awards conducted by the Sri Lanka Institute of Training & Development, where Access Engineering received a Silver award.
A total of Rs. 13.1 Mn was spent on training and development in 2013/14.
The average duration of training per employee during the year was 11h 37min for males and 11h 59min for females. The average training hours per year per employee by employment category were 11h 01min for staff and 09h 11min for workers.
Welfare Initiatives
The following welfare initiatives were conducted for our people in 2013/14: annual staff outings for the four divisions, the annual Christmas carnival on 12th December 2013 the daily distribution of morning and evening snacks free of charge to all employees, free health-screening programmes for labourers (a total of six programmes for the year), and a distribution of T-shirts among employees.
Health and Safety
The Company’s goal is to achieve a respective rate of <1 fatalities, major injuries and occupational-disease diagnoses per 200,000 person-hours of operation among its employees and members of the public. We are proud to state that this goal was achieved in the year under review.
Accidents, Occupational Diseases and Fatalities - 2013/14
Total Safety Hours | 16,487,603 | Fatalities | 0 |
Major Accidents | 4 |
Minor Accidents | 6 |
Frequency of Major Accidents | 0.0485 (<1) |
Frequency of Minor Accidents | 0.072 (<1) |
Health and Safety Practice
Employees are educated on standard operational procedures and the relevant safety precautions to take when carrying out different types of hazardous work. Guidance in the form of signage, etc. helps them identify and avoid unsafe practices and conditions.
Similar guidance is provided to enable employees to identify possible emergency situations. Emergency-preparedness plans are drawn up for every work-site and situation, and all employees receive training in first-aid and fire-fighting.
At every Access Engineering project and plant, health and safety (H&S) committees are set up and their members trained to implement H&S best practice.
Special H&S programmes target manual and unskilled workers, who are exposed to a statistically greater risk of accidents and occupational diseases. We also carry out health-screening programmes for these workers: a total of 156 were screened in the year under review.
Spending on Health and Safety
Safety precautions and health-screening programmes were the primary H&S cost components in 2013/14. The relevant figures are given below:
Health Screening Programmes - 2013/14
Site | Employees Screened | Cost (Rs.) |
Veyangoda Flyover Project | 28 | 67,000 |
Vavuniya Quarry and Crusher | 25 | 46,614 |
Polduwa Bridge Project | 23 | 8,490 |
Mechanical Workshop - Ranala | 35 | 9,750 |
UDA Building Project | 20 | 12,096 |
Rehabilitation of Labugama Kalatuwawa Water Treatment Plants Project | 25 | 7,500 |
Total | 156 | 151,450 |
Expenses incurred in relation to safety initiatives (consisting mainly of safety equipment and other tools): Rs. 48,8 Mn.
Education, training, counselling, prevention and risk-control programmes conducted for employees, their families, or community members regarding serious diseases are detailed below:
H&S Training - 2013/14
Programme | Type | Dates | No. of Participants | Agg. Trg. Hrs. |
Diploma in Occupational H&S | External | February - November 2013 | 4 | 1,280 |
Legal Aspects of H&S | Internal | 23rd March 2013 | 45 | 360 |
General H&S Training | Internal | March - April 2013 | 373 | 2,984 |
Workshop on Ergonomics | External | 11th July 2013 | 4 | 32 |
Workshop on ISO 9001:2008 Quality-Manual Preparation | External | 25th - 26th July 2013 | 1 | 16 |
General Training in H&S | Internal | October - December 2013 | 300 | 4,800 |
Health Hazards in the Construction Industry | Internal | 8th, 21st & 28th November 2013 | 110 | 880 |
First-aid Training | Internal | 19th - 20th December 2013 | 95 | 760 |
Health Monitoring and Reporting | Internal | 30th - 31st December 2013 | 50 | 400 |
ISO 14001:2004 Standard for Supervisory Grades | External | 26th February 2014 | 12 | 96 |
The impact of our H&S initiatives is reflected in a staff retention rate of around 94% - unheard of in the construction industry - and a lost-time injury frequency rate (LTIFR) of 1.088%, a further improvement over the 2012/13 figure of 1.2%.
Future Plans and Strategies
Recruitment
Our policy, going forward, is to recruit entry-level staff as management trainees and develop their management potential over time. In the case of geographically distributed projects and facilities, we seek, as far as possible, to recruit suitable people from surrounding communities. However, on foreign projects with a lot of value engineering, it is our preference to recruit Sri Lankan staff to work on these assignments.
Retention
The scheme of performance-based incentives will help sustain our already very high employee retention rates. We also seek to expand opportunities for skills development by taking on challenging new projects on which employees will have the opportunity to become adept at the use of new techniques and technologies.
Recognition
The growth and expansion of the business present an excellent opportunity for the recognition of our employees and plans are afoot to recognize and reward key performers.
Training and Development
In the future, there will be an enhanced role for training and development as a pillar of an HR strategy designed to promote productivity, technical competence and human resource retention. With this in mind, during the year, we constructed an in-house training facility that could house more than 150 employees at once. This facility is intended to cater to all our future internal training requirements.
Besides training in work skills and technical competencies, we will place increasing emphasis on training to assist employees in understanding and responding to the needs of the public and the individual communities they serve.
Since training is a key element in the development of suitably qualified individuals to support succession planning, we strive to provide equitable access and ensure the participation of all our people in training and appraisal. Whether or not an employee is chosen to be groomed for succession, this will ensure optimal performance and the realization of his or her full potential.
Health and Safety
We will continue with health screening for all members of our labour force. August 2014 will see the commencement of our second annual ‘Healthy Heart’ campaign, in which employees are taught about cardiovascular risk and how to avoid it.
Safeguarding Human Rights
Our membership in the UN Global Compact reflects our determination to uphold, respect and protect human rights. We have, through our contracted projects as well as self-initiated community programmes, helped provide basic amenities, healthcare and education; in addition, we provide decent and gainful employment to thousands of people through our operations.
We do not discriminate with respect to ethnicity, religion, gender or sexual orientation in selecting people for recruitment, training or promotion. Periodically we upgrade our policies with respect to recruitment, selection and placement, training and development, discipline and grievance management to ensure full compliance with this policy.
There were no incidents of discrimination due to gender, race, ethnicity, etc., reported in the year under review.
Child Labour: A Serious Issue
When entering into agreements with suppliers and subcontractors, we ensure that our partners are free from any taint of suspicion with respect to human rights abuses.
In our industry, there have been instances, even in the relatively recent past, where child labour has been used in quarrying, crushing and road-building; lamentably, such abuses have a long tradition in South Asia. Access Engineering is uncompromisingly opposed to all such practices and strictly prohibits suppliers and subcontractors from engaging in them. Stringent screening ensures that we do no business with organizations that exploit children as labour.
Business Partner Capital
Synergistic relationships with business partners have resulted in capital formation that benefits both Access Engineering and its partners. The following is a review of our business partnerships in 2013/14, together with an analysis of the growth in the value of such partnerships.
Strategic Alliances
- Access Engineering PLC tied up with ZMPC, the world’s largest manufacturer of port and container handling equipment (85% market share) to supply, repair and maintain container-handling equipment at Colombo Port (South).
- In partnership with China Harbour Engineering Corporation (CHEC), the Company embarked on its first international venture, the creation of a tidal basin to improve the capacity of the Port of Lae in Papua New Guinea.
- The Company was involved in a number of joint ventures with multinational contractors carrying out work in Sri Lanka in the year under review.
Besides delivering business and bottom line growth, these initiatives have resulted in the transfer of valuable knowledge and technology. A few examples of this are the ability to build steel flyovers and composite bridges, horizontal direct drilling and cable jetting. In the future, we will expand the ZPMC joint-venture model to other regions of the world, venturing into more overseas projects where we see opportunities for value addition and the transfer of knowledge and expertise to Access Engineering from its principals.
Growth in Joint Ventures and Subcontracting, 5 Year Analysis (Rs. Mn)
Sector | 2013/14 | 2012/13 | 2011/12 | 2010/11 | 2009/10 |
JV | 814.24 | 852.04 | 453.40 | 717.61 | 734.92 |
Subcontractor | 817.39 | 1,353.56 | 3,589.33 | 6,290.79 | 6,240.17 |
Social & Environmental Capital
Corporate Citizenship
At any given time, Access Engineering is involved in a number of community development and corporate citizenship projects. These are undertaken for the joint benefit of the organization and its stakeholders, for what is good for the people of Sri Lanka is ipso facto of benefit to a company which depends so closely on the economic development of the nation for its own future growth and prosperity. However, these projects reflect more than enlightened self-interest, because AEL is a proudly Sri Lankan enterprise with a heartfelt commitment to the land and its people.
A total of fifteen CSR projects were undertaken in the year under review. Many of these were of considerable duration and involved a sizeable investment of company resources. A breakdown of these projects by ‘platform’ or category is given below, followed by a more detailed descriptive analysis of each project.
CSR Projects by Platform - 2013/14
CSR Platform | No. of Projects |
Local Community Development | 2 |
Human Capacity-Building | 4 |
Health and Wellness | 3 |
Industry Advancement | 2 |
Environmental Stewardship | 4 |
Total | 15 |
CSR Projects in Detail - 2013/14
Category | Project | Description | ||
Local community development | Drinking water facilities for schools | Installed drinking water facilities at two rural schools in the Batticaloa District. | ||
School items for needy children | Donated items such as books, stationery, school bags, uniforms, etc., to 100 schoolchildren in the Ranala area. | |||
Human capacity-building | Mentoring programme for engineering students | Developed and sponsored a mentoring programme for students from the Civil and Earth Resource Departments of the Faculty of Engineering, University of Moratuwa: a total of 175 students. The programme included guest lectures, mentoring sessions with corporate executives, a weekend retreat, feedback from lecturers and an awards ceremony. Access Engineering provided sponsorship and inputs to improve the programme. Guest lecturers were sourced via a specialist firm, Image Consultants. | ||
Scholarships for employees’ children | Scholarships were awarded to employees’ children who received the highest Grade 5 Scholarship and GCE Ordinary Level examination results. | |||
‘Skills for success’ | A series of career guidance and skills development programmes in Jaffna, Mannar and Batticaloa for a total of 100 school leavers. The curricula included general ICT skills, English for the workplace and success skills. General career guidance was offered to the participants, with a leaning towards the construction industry. At the end of the 10-day programme, we conducted job interviews with participants we identified as prospective employees. The most promising candidates were offered scholarships to follow work-focused training programmes. The training programmes were conducted by Skills for Success (Private) Limited. | |||
Special instruction for primary school pupils | A demonstration on the proper use of technical equipment for children at Diddeniya Primary School, Hanwella. | |||
Health and wellness | Sessions on the dangers of substance abuse | A number of awareness-raising sessions on the dangers of alcohol, drug and tobacco abuse were held for employees in connection with World No Tobacco Day 2013. | ||
Dengue prevention programmes | Awareness programmes were conducted in suburbs around Kaduwela. | |||
Dengue eradication at schools | A programme was conducted to eliminate mosquito breeding sites in and around schools in the Colombo municipal area. | |||
Industry support | Employment support for the rehabilitation of former LTTE fighters | The development of the Sri Lankan construction industry is an issue close to our hearts. One of the main issues currently faced by the industry is a scarcity of skilled workers. To help rectify this - and, simultaneously, promote national reconciliation - the Company, in collaboration with the National Apprentice and Industrial Training Authority (NAITA), organized and successfully completed a training programme by means of which 32 former LTTE cadres acquired construction-related skills such as masonry and carpentry. Access Engineering donated course and assessment materials, paid the lecturers’ fees and provided tool kits for the trainees; we also underwrote the ceremony at which successful participants received certificates in their new skills. | ||
HDD demonstration | A demonstration on horizontal directional drilling was held for the IESL Uva Chapter in February 2014. | |||
Environmental stewardship | Learning event: ‘sustainable living through home gardening’ | An educational workshop on organic farming for Access Engineering employees, held to commemorate World Environment Day 2013. | ||
Paper recycling | Collecting and recycling paper waste through a registered service provider (570kg recycled in 2013/14). | |||
Tree-planting programme | An ongoing tree-planting programme where, on average, 150 trees are planted and maintained every month at and around the sites of completed or soon-to-be-completed projects. |
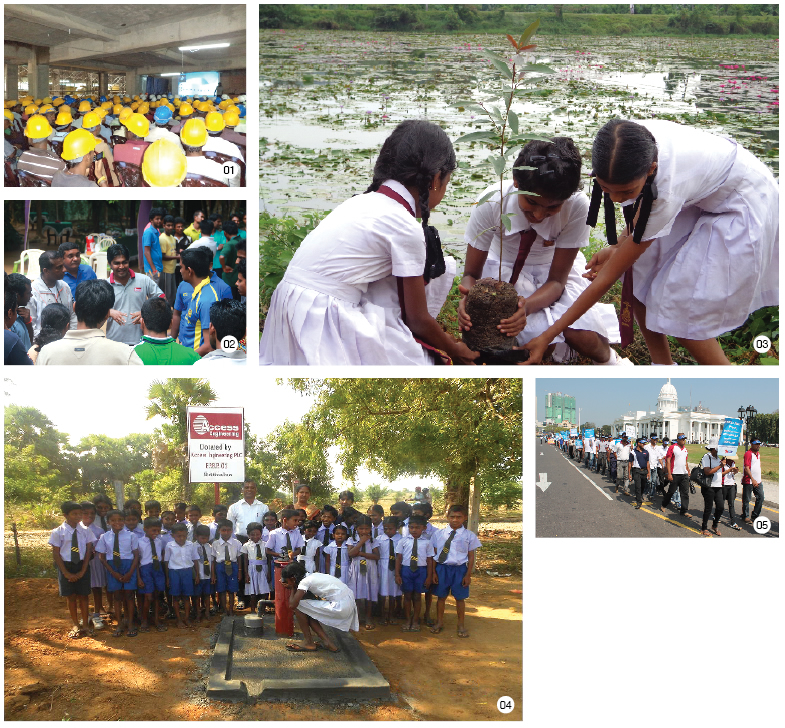
01. ‘World No Tobacco Day’ Awareness Programme
02. Mentoring Programme of the University of Moratuwa
03. Tree Planting Campaign
04. Programme for Providing Drinking Water Facilities
05. Dengue Awareness Walk
The Company has pledged its commitment to a district-wide vision-care programme for children in the Trincomalee area in 2014. Project components include teacher training, eye clinics at schools and the distribution of eyeglasses to schoolchildren.
Anti-Corruption Measures
All business units (head office, PMD1, PMD2, PMD3) and operational projects were analyzed for risks related to corruption during the course of the financial year.
Access Engineering was involved in a total of 76 operational projects in 2013/14. ‘Operational’ is here defined as ‘begun, completed or ongoing during the year’. Projects within the defect-liability period and still generating revenue are included in the definition, as are all the Company’s service units such as its mechanical workshop and geotechnical laboratory.
- A project that has begun is one in which an official award has been made of the project to Access Engineering, physical work has commenced, or project staff have been mobilized on-site.
- A completed project is one in which physical work has been completed, project staff demobilized or the project handed over to the client.
- An ongoing project is one that commenced in an earlier year and on which work was still continuing at the end of the financial year.
- Projects within the defect liability (DLP) or financial contribution (FC) periods are, respectively, those during which the Company retains financial liability for defects in execution, and those in which a contribution is realized during the financial year. However, some projects completed several years ago still continue to contribute to the Company’s annual turnover. Those projects have not been considered below unless their DLP extended into FY 2013/14.
Operational Projects - 1st April 2013 - 31st March 2014
Completed | 16 |
Commenced | 9 |
Ongoing | 25 |
DLP/FC | 26 |
Total | 76 |
The Company recruited a total of 208 people in 2013/14. All underwent the Company’s orientation programme, in which, inter alia, our anti-corruption policies are introduced and employees receive training in vigilance and procedures. Since our total staff strength is about 2,570, this means that a total of about 8% of staff received such training. The remainder underwent similar training in previous years.
Commitment to External Initiatives
Access Engineering is a signatory to the UN Global Compact (UNGC). The Company is a member of International Organization for Standardization (ISO) on QMS (9001), EMS (14001), OHSAS 18001 and Mechanical Testing (17025), TRACE membership for anti-bribery compliance, Ceylon Chamber of Commerce Business and Biodiversity Platform, Institute of Construction Training and Development (ICTAD) and National Construction Association of Sri Lanka (NCASL). It is also a member of The Institution of Engineers (IESL) Sri Lanka Accreditation Board (SLAB) and has received ISO 14001:2004, ISO 9001:2008, OHSAS 18001:2007 certifications from Det Norske Veritas Management System.
Protecting the Environment
Minimizing the Environmental Impact of Our Operations
All projects undertaken by the Company have potential environmental impacts. The impacts of significant aspects of Company operations, together with the actions taken to mitigate them, are given in the table below:
Operations, Environmental Impacts and Mitigation - 2013/14
Significant Aspect | Environmental Impact | Mitigation | ||||||||||||
Dust from roadworks | Air quality degradation | Road watering | ||||||||||||
Dust from crusher plants | Air quality degradation | Water sprinkling and water jacketing | ||||||||||||
Oil waste from mechanical workshop | Water quality degradation | Water treatment and monitoring of water quality |
||||||||||||
Cement contamination from batching plant | Water quality degradation | Sedimentation and re-use of water | ||||||||||||
Organic waste (various sources) | Landfill expansion | Composting | ||||||||||||
Waste paper (office operations) | Landfill expansion | Recycling | ||||||||||||
E-waste (office operations) | Heavy-metal contamination | Recycling | ||||||||||||
Steel (workshops) | Landfill expansion | Recycling | ||||||||||||
Fuel/oil leaks and spillages from machinery | Ground and groundwater contamination | Secondary containment for oil storage | ||||||||||||
Fossil fuel use | Natural resource depletion | Strict monitoring and control Preventive and corrective maintenance of machinery and vehicles | ||||||||||||
CO2 | Air quality degradation Contribution to anthropogenic climate change | Emissions testing Preventive and corrective maintenance | ||||||||||||
Noise from generators | Local nuisance | Soundproofing | ||||||||||||
Tree-felling during roadworks | Carbon sink destruction Degradation of natural environment Biodiversity loss (knock-on effect) Contribution to anthropogenic climate change | Tree-planting programmes, No. of trees planted:
|
Energy Conservation
Initiative : Corporate Energy Usage Targets
Objective : Reduce actual electricity consumption by 2% of budgeted consumption for the year
Means :
- Site offices designed with natural ventilation to reduce use of fans and air conditioning
- Use of solar power to operate welding and drilling equipment
- Procurement of energy efficient machinery
- Procurement of LCD monitors for desktop computers, maximum use of power-management function on computers, promoting the use of laptop computers
- Meeting rooms isolated from central AC system
- Lighting system divided into several zones with separate switches
- Installation of a power-factor correction capacitor
- Installation of energy-efficient light bulbs (compact fluorescent lamps and LED)
Results : Shown below:
Measurement of Objective
Water Conservation
Initiatives for minimizing water consumption -
- Recycling and re-use of water at all our construction sites (as much as possible)
- Wastewater treatment plants installed to recycle contaminated water and reduce soil and groundwater contamination (e.g. at Mabima batching plant and Ranala workshop)
- More efficient water consumption by usage budgeting and setting advisory consumption limits
Water Use and Re-use - 2013/14 (Units)
Total water usage | 30,234,131 |
Annual usage per employee | 11,764 |
Monthly usage (average) per employee | 980 |
Water re-used and recycled units | 701,187 |
Percentage | 2.32% |
1 unit = 1,000 litres
Paper Conservation
Paper is a resource whose manufacture has considerable environmental impact. Access Engineering has moved to reduce paper consumption by setting a monthly consumption budget, using both sides of every printer paper and regularly recycling used paper with the help of our business partner Neptune Recyclers. Paper consumption is expected to reduce further with the implementation of the ERP system.
Waste-Management Best Practice
Non-hazardous construction and demolition (C&D) debris is used for landfills and C&D wood material for chipping. Solid waste is segregated into re-usable, recyclable and compostible waste and treated accordingly. A significant portion of used paper and concrete are recycled.
Fossil Fuel Conservation and Greenhouse Gas Emission Control
We strive to control greenhouse gas emissions and conserve fossil fuels to the fullest extent practicable. Among the methods we use to achieve this are, the use of solar-powered lamps to illuminate sites during night works as an alternative to diesel generators, the use of solar-powered service vehicles, the regular maintenance of all petrol and diesel fuelled vehicles and machinery to promote fuel efficiency, minimizing vehicle idling time by enhancing awareness among drivers, the use of appropriate-sized vehicles and equipment (for example, ensuring that large trucks are not used to transport small loads), and more efficient route and journey planning.
Energy and Materials Saved - 2013/14
Wastepaper Recycled (kg) | 570 |
Full-grown Trees Saved (No.) | 9 |
Oil Saved (l) | 1,001 |
Electricity Saved (kWh) | 2,280 |
Water Saved (l) | 18,114 |
Landfill Saved (m3) | 2 |
Reduction in Greenhouse gas Emissions (kg of Carbon Equivalent) | 570 |
Eco-Friendly Materials Usage and Work Operations
A variety of environmentally friendly practices and precautions govern our operations and use of materials. Among these are -
- taking appropriate precautions when handling and transporting construction materials, including readymix concrete and asphalt
- evaluating suppliers on the basis of their environmental practice
- training and familiarizing office staff, project workers, suppliers and subcontractors on environmentally friendly operations and practices
- ensuring that environmental degradation does not occur during transport, loading and unloading or storage of materials
- the use of a fluid de-sander, which facilitates the re-use of drilling fluid by separating sand and silt from the used fluid
- the use of wastewater for watering construction sites to avoid dust formation
- employing water-jacketing systems at quarries and crusher plants to minimize dust spread
- the use of effective secondary containment at fuel and lubricant storage sites
- the practice of appropriate storage and spill-management precautions when handling fuels and bitumen (as per standard operating procedures and work instructions)
- an emergency action plan for oil spills, with training and assigned roles for employees
- general implementation of the 3R (reduce, re-use and recycle) concept
- working with the National Cleaner Production Centre at our Kotadeniyawa plant to analyze water, energy and materials flows and make recommendations on potential resource savings and ways to enhance environmental performance.
- The transport of materials generates CO2 from vehicle emissions. The transport of ABC materials also generates dust. However, we have not been able to quantify or accurately estimate these impacts.
- Location and size of land owned, leased, managed in, or adjacent to, protected areas and areas of high biodiversity value outside protected areas:
- Vavuniya crusher and asphalt plant: 1 acre each
- Labugama: 5.3 hectares
- Kalatuwawa: 6.4 hectares
Environment Management System
The Company’s environment-management system (EMS) is periodically monitored and evaluated in terms of effectiveness by internal and external audits. The latter are carried out by the designated certification body, DNV.
Management of Customer and Stakeholder Complaints
Legal and regulatory non-compliance and external complaints are treated as the gaps in the EMS. As soon as the root causes are identified, corrective action is taken to prevent further contraventions. The effectiveness of these actions is evaluated through follow-up audits and management reviews.
Legal and regulatory compliance is promoted on a project-by-project basis by identifying all pertinent legal requirements and distributing lists of these round all our projects and plants. Training is also carried out on the subject. Compliance is monitored through internal reports and audits.
Effective Project Risk Management
Risk identification and mitigation plans cover risks associated with financial resources, work progress, environmental impacts, work quality, etc. The internal audit team communicates the importance of risk identification and mitigation to the relevant parties at the beginning of each project.
Costs and Impacts
Environmental Protection Expenditure - 2013/14
Measure | Cost (Rs.) |
Secondary Containment | 324,000 |
Tree Planting | 281,292 |
Water Treatment at Mechanical Workshop | 500,000 |
Piling: Mud-Bucket use at Access Tower II | 543,000 |
Truck Mixture Washing Facility | 50,000 |
Total | 1,698,292 |
- ISO 9001 QMS is compulsory to retain our ICTAD C1 grade. ISO 14001 & OHSAS 18001 will be essential qualifications for our assignment to the proposed ICTAD supra-grade category. These certifications will also improve our performance in tender competitions.
- Value engineering becomes more practicable with good environmental management, helping Access Engineering achieve its corporate vision and mission
- Cost reductions due to legal and regulatory compliance
- Compliance helps us meet the demanding requirements of funding agencies such as the World Bank and ADB, which focus strongly on environmental and social initiatives
- Avoidance of reputation risk
- Greater customer satisfaction
Future Plans and Strategies
Our commitment to community support and good corporate citizenship is ongoing. In 2014/15, we will continue our involvement in the Trincomalee District vision-care programme mentioned above.
In terms of resource conservation and waste management, we will implement a management programme to raise awareness of these issues through the display of appropriate signage and other measures at offices and work-sites. Measures to reduce paper consumption will be strengthened further. Focused e-waste management programmes will be conducted in 2014/15.
We are pledged to work towards better conservation of natural resources in collaboration with the Business and Biodiversity Platform of the Ceylon Chamber of Commerce, and will be involved in helping protect the country’s richest biodiversity reservoir, the Sinharaja Forest.
Finally, the day-to-day conduct of our business amounts to a CSR programme, since the projects we carry out are to the benefit of the general public.
General Legal and Regulatory Compliance
- Monetary value of significant fines and total number of non-monetary sanctions for non-compliance with environmental laws and regulations: No fines or sanctions.
- Total number of legal actions for anti-competitive behaviour, antitrust and monopoly practices and their outcomes: No legal actions were instituted against the Company in the above-mentioned categories.
- Monetary value of fines and total number of non-monetary sanctions for non-compliance with laws and regulations: The Company adhered to all applicable laws and regulations in 2013/14. No regulatory violations were committed, and therefore no fines or sanctions were levied.